How to Increase Output on an Assembly Line?
Selim Reza
25 Aug, 2024
Reducing line Setting Time for an Assembly line in the Apparel Industry is crucial for Maximizing Efficiency and Productivity.
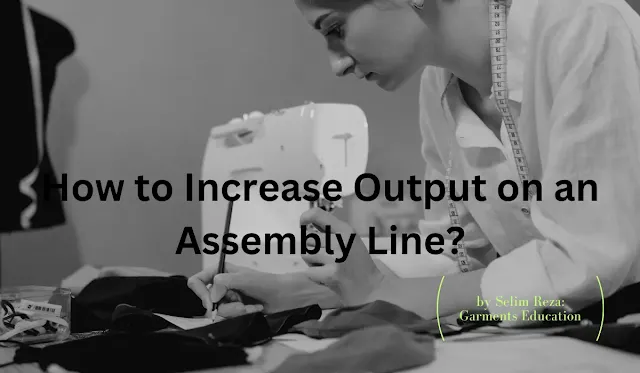
How to Increase Output on an Assembly Line? Here are strategies to help minimize the time required to set up an assembly line:
1. Pre-Planning and Preparation:
- Detailed Planning: Plan the line setup in advance by analyzing the production order and determining the most efficient layout for machines, materials, and personnel.
- Standard Operating Procedures (SOPs): Develop and implement SOPs for line setting, which provide clear, step-by-step instructions for the process.
- Mock Setups: Conduct mock setups or simulations to identify potential issues and refine the process before the actual line setting.
2. Standardization of Tools and Equipment:
- Tool Standardization: Use standardized tools and equipment across different lines to reduce the time spent on searching for or adjusting tools.
- Pre-Set Machines: Pre-set sewing machines, cutting tools, and other equipment to the required specifications for the new style before the line setting begins.
3. Organized Workstations:
- 5S Implementation: Apply the 5S methodology (Sort, Set in order, Shine, Standardize, Sustain) to organize workstations, ensuring that everything needed is easily accessible and in its place.
- Pre-Positioning Materials: Ensure that all required materials and components are pre-positioned at the workstation before line setting begins.
4. Efficient Workflow Design:
- Line Balancing: Design the line to balance the workflow, ensuring that tasks are evenly distributed among workers and machines to minimize idle time.
- Modular Layouts: Use modular layouts where possible, allowing for quick reconfiguration of workstations to accommodate different products or processes.
5. Use of Technology:
- Line Setting Software: Utilize software tools that help in planning and simulating line setups, allowing for quick adjustments and optimal configurations.
- Digital Work Instructions: Provide workers with digital work instructions that can be easily updated and accessed, reducing setup time and errors.
6. Training and Skill Development:
- Cross-Training Workers: Train workers to be proficient in multiple tasks so they can assist in setting up various parts of the line quickly.
- Line Setting Teams: Develop specialized teams trained specifically in line setting, capable of executing the setup process efficiently.
7. Parallel Activities:
- Simultaneous Setup: Conduct parallel setup activities where multiple aspects of the line are being set up simultaneously (e.g., while one group sets up machines, another group can prepare materials).
- Pre-Assembly: Pre-assemble components or sub-assemblies in advance to reduce setup time on the main assembly line.
8. Quick Changeover Techniques:
- Single-Minute Exchange of Dies (SMED): Implement SMED techniques to reduce changeover time by preparing and simplifying the steps required for line setting.
- Quick-Release Fixtures: Use quick-release fixtures and clamps on machines and workstations to enable faster adjustments and setups.
9. Effective Communication:
- Clear Communication Channels: Establish clear communication channels between the production planning team and the line workers to ensure everyone is aware of the setup requirements and timelines.
- Real-Time Updates: Provide real-time updates to the team regarding any changes in production plans or line settings.
10. Continuous Improvement:
- Kaizen Events: Conduct regular Kaizen events focused on reducing line setting time, where workers can suggest improvements and innovations.
- Performance Tracking: Track and analyze line setting times for different setups, and identify patterns or areas for improvement.
11. Use of Templates and Jigs:
- Standard Templates: Develop and use standard templates for line setups that can be quickly adapted to different products or styles.
- Custom Jigs: Create custom jigs and fixtures that can be used across multiple setups to reduce the need for adjustments.
12. Post-Setup Audits:
- Setup Audits: After setting up the line, conduct quick audits to ensure everything is in place and functioning correctly, reducing the need for time-consuming corrections later.
Summary:
Implementing these strategies, you can significantly reduce line setting time, leading to faster production Starts, Improved Efficiency, and Increased overall Productivity in the Apparel Manufacturing Process.